Da sempre in Progetti lavoriamo per la promozione di un uso razionale dell’energia, impegno che si traduce in un duplice obiettivo: assicurare un consistente risparmio economico ai nostri clienti e contribuire alla riduzione dell’impatto ambientale dell’industria. Un aspetto, quest’ultimo, sempre più rilevante se consideriamo la sfida che l’industria della ceramica, notoriamente molto energivora e inserita non a caso tra i settori “hard to abate”, è oggi più che mai chiamata ad affrontare. Un altro aspetto importante è la ricerca di un’innovazione tecnologica funzionale alla crescente attenzione verso la qualità dell’ambiente di lavoro e al raggiungimento di standard di sicurezza sempre più elevati.
La volontà di trasformare tutte queste sfide in opportunità per essere concretamente sostenibili è al centro del progetto che abbiamo realizzato assieme al nostro storico cliente FV Area Andina S.A., azienda ecuadoregna leader nella produzione della ceramica sanitaria.
Il progetto ha preso avvio da un’esigenza specifica: implementare nel processo produttivo un essiccatoio continuo che fosse moderno ed efficiente, sotto il profilo della produttività e della sostenibilità.
I nostri ingegneri, lavorando in stretta sinergia con il team dell’azienda, hanno avuto la possibilità di sfruttare al massimo le potenzialità del risparmio energetico: a partire da una valutazione a 360° del processo produttivo e dopo un audit accurato (link articolo precedente), è stato possibile consegnare al cliente un essiccatoio continuo su misura che funziona letteralmente gratis, perfetto esempio di ingegneria energetica sostenibile.
L’azienda utilizzava precedentemente un essiccatoio intermittente, attivo 365 giorni all’anno. Inoltre, un’ampia area dello stabilimento era adibita a stoccaggio dei pezzi, i quali rimanevano depositati dai 3 ai 9 giorni per consentire il completamento del processo di essiccazione.
Per far fronte ad una maggior richiesta da parte del mercato e per ottimizzare i costi di produzione, al fine di essere ancora più competitivi sia dal punto di vista quantitativo sia qualitativo, si è scelto di intervenire nel processo di essiccazione con un nuovo impianto tecnologicamente avanzato.
Il primo passo è stato lo studio per verificare la fattibilità tecnica di un essiccatoio continuo che escludesse l’utilizzo del combustibile. L’analisi ha evidenziato la possibilità di recuperare per il funzionamento dell’essiccatoio ben 35.000 m3/h di aria secca generata dai forni a tunnel; a questa principale fonte di alimentazione si è aggiunto lo sfruttamento del calore di scarico in uscita dal camino con i gas di combustione, riutilizzabile tramite scambiatore di calore.
Sempre in ottica di una gestione eccellente dell’energia abbiamo studiato il riutilizzo dell’aria calda umida emessa dall’essiccatoio direzionandola nella sala colaggio per il mantenimento della temperatura nei parametri ideali.
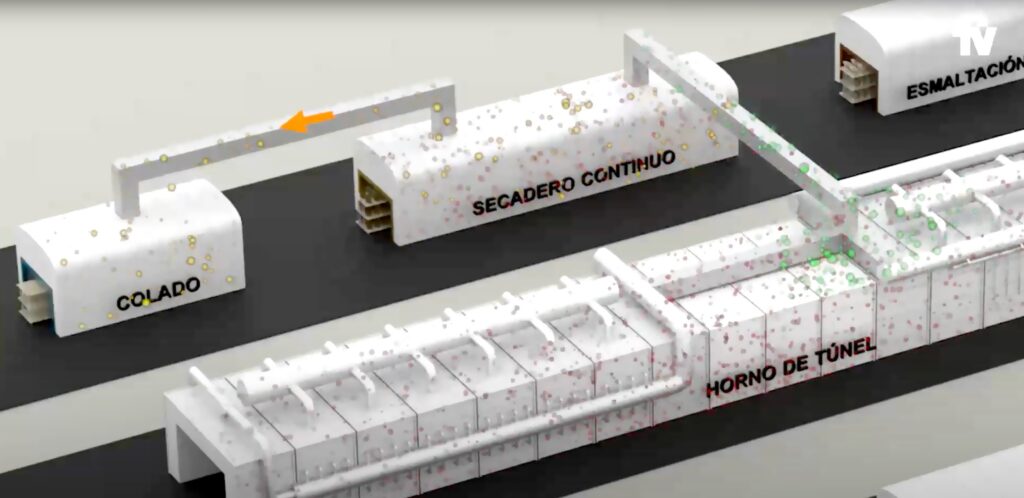
Una volta messo in funzione, il nuovo essiccatoio ha confermato i risultati attesi:
- alimentazione senza utilizzo di combustibile fossile, corrispondente a un risparmio annuo di 60.000 galloni di carburante;
- riduzione di circa 630 tonnellate all’anno di CO2 ;
- sensibile diminuzione delle ore di funzionamento della centrale termica per il riscaldamento della sala di colaggio;
- diminuzione dei tempi di essiccazione, passati da giorni a ore;
- liberazione dello spazio prima destinato ad area di stoccaggio, in quanto i pezzi escono dall’essiccatoio già pronti per le successive lavorazioni;
- aumento del rendimento e della qualità del prodotto grazie a un controllo ottimale dei parametri.
Tra i vantaggi del nuovo essiccatoio va sicuramente annoverata anche la forte automatizzazione, che ha permesso di sollevare gli operatori da buona parte dello sforzo fisico e di contenere la circolazione di macchine operatrici.
Sul fronte del risparmio energetico, accanto all’alimentazione dell’essiccatoio esclusivamente attraverso calore recuperato, sono state studiate soluzioni per limitare al massimo il consumo di energia elettrica richiesto per la parte di controllo elettronico e automazione.
“L’essiccatoio è stato realizzato in Italia e poi trasportato in Ecuador, dove Progetti ha supportato il cliente in tutta la fase di installazione e di start up – racconta Stefano Striolo, head of Progetti Ceramic Innovation – Una delle sfide principali è stata proprio la messa in opera dell’impianto senza necessità di interrompere la produzione”.
“Siamo molto soddisfatti di quanto realizzato ed è sempre molto stimolante poter lavorare come in questo caso con clienti che hanno una forte competenza specifica – spiega il CEO di Progetti Marco Lora – Per noi è molto importante mettere a loro disposizione il nostro know how ed aiutarli a portare avanti un paradigma di crescita virtuoso”.